|
|
Quiet Fans - Fan/Power control methods
|
Date Posted: Oct 25 2001
|
Author: Brians256
|
|
|
Posting Type: Article
|
Category: Electronics
|
Page: 1 of 1
|
Article Rank:No Rank Yet
Must Log In to Rank This Article
|
|
|
Note: This is a legacy article, imported from old code. Due to this some items on the page may not function as expected. Links, Colors, and some images may not be set correctly.
|
|
Quiet Fans - Fan/Power control methods By: Brians256
|
|
Keeping the Fans Quiet - Power Control Methods
|
|
By: Brians256 10/19/01
|
|
|
|
Quiet!
|
|
|
Fans are loud. Anyone using a computer has, at one time or another, been annoyed by the buzz, whine or outright shriek of cooling fans. Unfortunately, cooling is necessary, and even water-cooled computers use fans on their radiator. The key to a quiet computer fan is twofold: pick the right fan and minimize the noise from the fan. This article has some general background information about fan speed control, and then explains a PWM fan speed control circuit.
All the below information was gathered from different web articles, people on different overclocking and electronics forums, and a many great books. There are too many to mention, but several sources are mentioned throughout the article.
|
|
Before getting into some of the possible solutions, we should understand our subject. Maxim has a great article with more detail here: Fan Speed Control Is Cool! Another website, 7volts, has a good general article on making fans quiet.
Computer fans are usually 12V DC brushless fans with ball or sleeve bearings. The electrical motor uses current from the 12V input (two wires) to turn magnets on and off to create torque and thus produce fan rotation. When a motor is brushless, it means that there are electronic circuits in the motor that decide when the magnets are turned on and off. This reduces the number of moving parts, but can be a problem with some types of fan speed control. Ball bearing fans have a reputation for longer life, but it truly depends upon the manufacturer. Properly designed sleeve bearings can be extremely reliable. Thankfully, bearings are only noisy when they fail.
Fans can also provide feedback to a controller. Most PC fans have a third wire for monitoring RPM. That third wire connects to a Hall effect sensor, sending a pulse every half-revolution. As long as the fan is rotating and supplied with normal voltage, the RPM wire provides excellent feedback. Unfortunately, many speed control methods make this RPM signal inaccurate or even dangerous to the motherboard's fan speed sensors.
|
|
The fan speed can be controlled in a number of ways. The easiest way is to change the voltage. Half the voltage means half the speed. Many overclockers use larger faster fans at 5V or 7V to produce the same CFM as smaller 12V fans. Using a reduced fixed voltage is the easiest path to quiet your fans, because the PC power supply already produces several voltages.
|
|
|
|
The 4-pin Molex connectors contain both 12V and 5V power, so it is easy to hook a fan up to the 12V line, the 5V line, or 7V. This method has been covered many times by several web sites. Normally, the fan has a black wire (ground) connected to a corresponding black wire in the Molex connector, and a red or yellow wire connected to the yellow (+12V) wire in the Molex connector. You can see the Red (+5V), Black (Ground), Black (Ground) and Yellow (+12V) wires going to the Molex.
|
|
|
|
|
Fan Wire 1 (Black)
|
Fan Wire 2 (Red or Yellow)
|
Fan at 5V
|
Molex Ground (Black)
|
Molex +5V (Red)
|
Fan at 7V
|
Molex +5V
|
Molex +12V (Yellow)
|
Fan at 12V
|
Molex Ground (Black)
|
Molex +12V (Yellow)
|
|
|
For example, to run the fan at 7V, connect the fan's black wire to the +5V (Red) Molex connection and the fan's red/yellow wire to the +12V (Yellow) Molex connection. You can connect the fan's RPM wire directly up to the motherboard.
For information about how to connect a Molex connector to a fan, look here: Molex Connection. For tutorials about different fan voltages, look here: ATX Notes.
- Good: This is simple and cheap. Many people are happy by changing their noisy fans to 7V.
- Bad: No control after it is hooked up! Many fans won't run at 5V, or they are nearly useless.
|
Variable Voltage - Rheostats
|
|
The next step is to control the fan voltage dynamically, and this can be accomplished in a number of ways. Rheostats and voltage regulators are the most common. A common PC mod (called the BayBus) uses a bank of rheostats to vary the voltage going to different fans. A voltage regulator performs the same action, but is much cheaper, because high-wattage rheostats are more expensive than a voltage regulator plus a low-wattage rheostat.
|
|
|
|
With a rheostat, there are three connections. To control fan speed, we only need two of those. We use the middle connection and one of the outer ones. Truthfully, I do not know which one you will need on your particular rheostat. If you look at the picture below, I used the middle and right connections. The middle connection was hooked up to the 12V connector of the Molex and the right-hand connection was hooked up to the fan's red/yellow wire. The fan's black wire was connected to the black (ground) wire of the Molex connector.
|
|
|
|
That causes the resistance to drop as I turn the knob clockwise. The lower the resistance, the higher the voltage, and the faster the fan goes. Typically, you will want a 1 Watt rheostat or better, with about 100 Ohm maximum resistance. Take a look here for a tutorial on using rheostats. Or, at the OCMod website, this article is even better.
This was an OK solution, and it works well for most people. Unfortunately, I am a perfectionist. If you run the fan at less than 12V, the rheostat is dumping heat inside your PC! Also, you have to manually adjust it yourself, and I want my computer to take care of itself. However, people (including myself) that like blinking lights and lots of knobs will love this case modification.
- Good: This is still very simple, it works well, and it looks very spiffy.
- Bad: Waste heat and lack of automation.
|
Variable Voltage – Voltage Regulators
|
|
The voltage regulator is an alternative to the high wattage rheostat. By using a voltage regulator (the LM317), we can use a smaller wattage rheostat or we could even add automation. The PC will be able to cool itself as much as it needs and no more. Finally, this is a solution that is always as quiet as it can be, but never sacrificing performance. If the PC is working hard, the fans work harder to cool the computer. Perfect! Right? Well, no.
There are several tutorials on using the LM317 voltage regulator. For a start, this shows how to use a rheostat and an LM317 to create a great fan control. Uller (Ryan Myers) wrote the best article I have seen on the basic circuit. Here is another article at the OCMod site that shows a very compact implementation. Here is a great article on how to use the LM317 to control many fans. Here is a great circuit that adds an NTC thermistor to the standard LM317 circuit, removing the need to manually adjust the fan speed. The OCMod circuit is the cheapest variation, but it is a pain to adjust.
Some major drawbacks exist, however. First, the voltage regulator does not allow the full voltage range. Second, whenever the voltage regulator is restricting the voltage, the excess energy is being dumped (as heat) into the computer.
If you start out with 12V, the voltage regulator cannot pass that full voltage through itself; some voltage is lost. In fact, the maximum voltage possible with the LM317 is about 10.75V. In some cases, the voltage does not reach above 9.5V. Some people use a secondary switch to bypass the regulator when they want full 12V speed. But, this is still more complex than the simple rheostat circuit. Also, a fan, which might run at 3V, may not be able to start at 3V. The current required to start a fan at low voltages is much larger than required at a full 12V. The result is a stalled motor: no movement. A voltage regulator thus cannot support the full speed or the low speed for a fan.
- Good: Can be automated with thermistor, can be compact, can be cheaper than rheostat, and is fun to assemble. This one can look just as neat as the rheostat case modification.
- Bad: More complex than rheostat, dumps heat into computer, and it cannot use the full range of fan speeds.
|
Variable Duty Cycle – PWM Speed Control
|
|
|
This is my favorite method, mostly because it has such interesting theory behind it. PWM stands for Pulse Width Modulation and it works by turning the fan on and off very rapidly, but at full voltage. If you turn the fan on 100 times a second (100 Hz), and leave the power on for 1/200th of a second, you are providing 50% of the normal power (the power is on half of the time). This is a 50% duty cycle. Leaving the power on all the time is a 100% duty cycle.
|
|
Below is a sample trace of the voltage being sent to a fan with my PWM controller. I used a TPI multimeter/scope to look at the circuit, and it is currently showing a 50% duty cycle. You can see how the voltage is only high for half of the time. The frequency is about 18 Hz, which is very low, but it doesn't whine. I'll probably change that frequency to 80Hz when I get more time to tinker with it. That is simply done by replacing the 0.47µF capacitor (C1) with a 0.1µF capacitor.
|
|
|
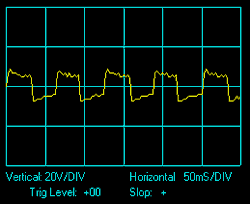 |
|
|
|
|
|
The PWM circuit that I built is based mainly on remarks and assistance from Uller, the designer of LCDriver (a free software package used to run LCD's and VFD's from a PC serial or parallel port). He has an extensive self-taught knowledge of electronics, and gave me the general outline of the circuit as well as answering specific questions.
|
|
|
|
Above is the circuit. Basically, there are three main sections: the frequency generator, the PWM signal generator, and the power control. The frequency generator produces a fixed frequency saw-tooth wave. The PWM signal generator uses the fixed frequency saw-tooth wave along with a variable input voltage to produce a variable duty-cycle square wave. The power control uses that square wave to control the power sent to the fan, since the PWM signal generator (the 741 op-amp) cannot supply enough current to power a fan.
|
|
The frequency generator is based upon the 555 chip, and is composed of R1 (56K), R2 (56K), C1 (0.47µF) and U1 (555 chip). The 555 chip turns voltage on and off to the capacitor, alternately ramping the voltage and discharging the voltage. If you use a scope and take a look at the voltage (in reference to ground) at pin 2, you get a nearly saw-tooth waveform like this:
|
|
|
|
I chose two handy resistors and then calculated a capacitor value that would give me a certain frequency. The 555 chip comes with a sample circuit when you buy it from RadioShack, but you can also find a 555 Calculator on the web that can do all the calculations for you. There are several other calculators out there if you do a quick search. Basically, frequency is:
Frequency = 1.44 / ((R1 + R2 + R2) * C1)
Notice, however, that I'm using the 555 in an unorthodox manner. The 555 has output on pin 3, but I leave it totally unconnected. That is because the 555 is configured to produce a square wave output. The voltage across the capacitor is a nearly perfect saw-tooth wave, which is perfect for the next stage of the circuit: the op-amp. It ranges from 1/3 of Vcc to 2/3 of Vcc(4V to 8V).
The 741 op-amp compares the saw-tooth wave against a reference voltage and produces a low voltage when the saw-tooth wave is above the reference, and a high voltage otherwise. The result is a square wave (either on or off) of constant frequency. The higher the reference voltage, the more time the 741 output stays high. If you swap the inputs of the 741, you get the reverse effect.
The reference voltage supplied on pin 3 of the op-amp is defined by the ratio of R3 to R4.
Vref = (Vcc * R4) / (R3 + R4)
Vcc is the power supply voltage, which is 12V in this case. R3 is a rheostat which can go from 0 Ohms to 10K Ohms. So, Vref can range from 12V to 4V. I picked that bottom number on purpose, because I don't need to compare any lower than the bottom of my saw-tooth wave. If the reference voltage is 4V (the rheostat is all the way conducting), the op-amp output is always off (zero speed for the fan). If the reference voltage is above 8V, the op-amp output is always on (full speed for the fan).
|
|
The next step would be to use some wizardry to ensure that the reference voltage does go above 8V (because there is no need to compare to anything more than 8V). That would make the rheostat less touchy and use its full range. The simplest method reduces the voltage in two stages. The first reduces the 12V to 8V with a voltage divider (adds two resistors: 4K and 8K Ohm). Then second stage (changing the pot/rheostat to 5K Ohm instead of 10K Ohm) then can vary the voltage from 4V (halving the 8V input) to 8V (allowing the 8V to pass through).
The output stage is designed to take that PWM square wave and boost the current carrying capacity. At first, I used only two components: the N-Channel MOSFET and a diode. A MOSFET transistor is great for switching power. When it is on, there is very little resistance, which means no heat is generated. When it is off, it is really off. No wasted energy. This is why the PWM circuit is so efficient. The requirement for the diode is not obvious. The diode runs parallel to the fan and conducts electricity in the opposite direction. Why?
Electrical motors are huge inductors. So what, you exclaim! Well, inductors resist
|
|
|
|
changes in voltage, and the PWM circuit is changing from 0V to 12V very quickly. At every change (in either direction), the fan motor's inductance sends a huge voltage (low current, so it's not dangerous) spike in the reverse polarity, trying to stop that voltage change. MOSFET transistors blow out when they are reverse biased like that. So, the diode provides a safe bypass for that inductive response. When the MOSFET is non-conducting, the fan sends voltage toward the MOSFET, but it is absorbed by the diode and sent back to the "top" of the fan. Actually, this makes the circuit more efficient. That inductive energy spike is recycled into the fan to keep it running a bit longer.
It didn't work. I asked Uller, and he gave me a nearly incomprehensible reply, "I think the problem lies in the uA741's output voltage swing, and the fact that the falling threshold on the 540 is so high." Well, I used a IFR510, not a 540, but the principle should be the same. Solution? Uller replied, "Have you tried feeding the 741 output to an NPN, and having the NPN drive the FET?" Well, no. Why shouldn't the 741 suffice? After all, a MOSFET isn't drawing much current (almost none), and the 741 should interface quite nicely. Well, it turns out that Uller was correct. Almost.
It still didn't work. I guessed that the NPN transistor wasn't allowed to pass a sufficient current through itself. After all, a bipolar transistor conducts current from emitter to collector. My NPN collector was connected to the MOSFET gate, which does not absorb any current to speak of. So, I added a high-resistance path to ground to allow some leakage. That is R5, the 56K resistor.
It STILL didn't work! Well, I didn't tell you that I was connecting the fan "below" the MOSFET. The MOSFET was connected to +12V on one side and the fan on the other. Uller gave me another hint, "Driving on the high side requires more gate voltage than low side. With MOSFET's, the threshold voltage is relative to the source, not the drain - so if you drive high, the threshold voltage is going to be higher relative to ground than if you drive low." Well, OK. I changed my circuit so that the MOSFET was connected to the fan and GROUND; this is called low-side control.
It worked! OK, now I'm mostly happy with the result. I'll probably change the capacitor to increase the frequency, and I'll probably change the reference voltage portion to use a thermistor. A thermistor will be attached to the radiator. Oh, didn't I tell you? It's for water-cooling, of course.
- Good: Efficient use of power and full range of fan control.
- Bad: Complicated and expensive.
|
|
If you have any comments or Questions please email me at Brian_Smith@cmicro.com
|
|
|
|
Random Forum Pic |
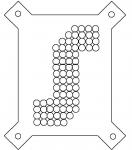 |
From Thread: Opinions on my design |
| ProCooling Poll: |
So why the hell not? |
I agree!
|
67%
|
What?
|
17%
|
Hell NO!
|
0%
|
Worst Poll Ever.
|
17%
|
Total Votes:18Please Login to Vote!
|
|