|
|
Swiftech MCW-Chill452 Review
|
Date Posted: Apr 27 2004
|
Author: pHaestus
|
|
|
Posting Type: Review
|
Category: H2O and High End Cooling Reviews
|
Page: 1 of 3
|
Article Rank:No Rank Yet
Must Log In to Rank This Article
|
|
|
Note: This is a legacy article, imported from old code. Due to this some items on the page may not function as expected. Links, Colors, and some images may not be set correctly.
|
|
Swiftech MCW-Chill452 Review By: pHaestus
|
|
Chilled water presents many advantages to the PC enthusiast. Processor temperature in a water cooling loop is dictated by several factors: the TIM joint,
the waterblock's efficiency, and coolant temperature. By chilling the coolant, one can dramatically lower processor operating temperature.
|
|
Additionally, chilling the coolant in an existing cooling loop provides a method of cooling a system's GPU and northbridge extremely
effectively. There are many examples of recirculating chillers in both industrial and laboratory applications and the technology is quite robust in these sectors. Both phase-change and solid state
(thermoelectric) water chillers are available commercially for applications ranging from medical to the cooling of high power lasers. In the PC water cooling community, however, only phase-change water
chillers have typically been commonly considered successful. Swiftech has now produced a commercial chiller, the MCW-Chill 452, which utilizes two 226W peltiers to chill coolant. This product was
originally designed for industrial applications,
|
|
|
|
but is now sold on their website to anyone with ~ $300US. Bill Adams of Swiftech was kind enough to loan us a MCW-Chill for (protracted) testing
|
|
|
|
|
|
|
|
|
|
|
|
|
The MCW-Chill is a water chiller that has been produced largely from standard Swiftech waterblock parts. At first glance it seems to be a couple of
MCW5002 waterblocks cooling peltiers. The cold side of the peltiers are in turn cooling a small chamber where water is chilled. And this is true, but other Swiftech parts lurk inside the insulation.
A diagram should be helpful in demonstrating how the MCW-Chill is put together:
|
|
|
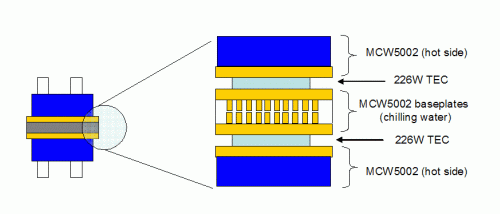 |
|
|
Instead of traditional cold plates, the MCW-Chill uses baseplates from MCW5000 waterblocks. This dramatically increases the surface area exposed to the
water on the cold side and is one of the keys to the MCW-Chill's success.
Every overclocker should want chilled water; it's the logical step up from water cooling and can, if put together correctly, handle a CPU, GPU, and
northbridge. In the case of the MCW-Chill, there is definitely enough headroom for cooling all your system's hot bits. But while dual 226W peltiers may chill water quite effectively, there is a
downside: You now have to cool those peltiers! No free rides here guys; look forward to dissipating well over 500W total heat and using a lot of electricity to power the peltiers. And even if that doesn't scare
you away, there's still the issue of space. And you'll need a lot of water cooling parts: 2-3 complete cooling loops in fact. When I set up the MCW-Chill, I opted to cool each 226W peltier with a separate
loop. I think that I made the right choice as performance was quite good and going overboard on cooling is always fun. This meant, however, that I required 2 large heatercores, 4 100CFM 120mm fans, two 300GPH pumps,
and a lot of ½" hose for the two hotside loops. In addition, a smaller pump, CPU waterblock, and 3/8" hose were needed for the chilled loop. My final cooling loops looked like this on paper:
|
|
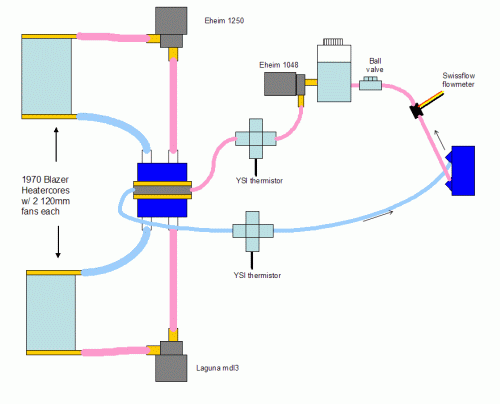 |
|
|
And like this in practice:
|
|
|
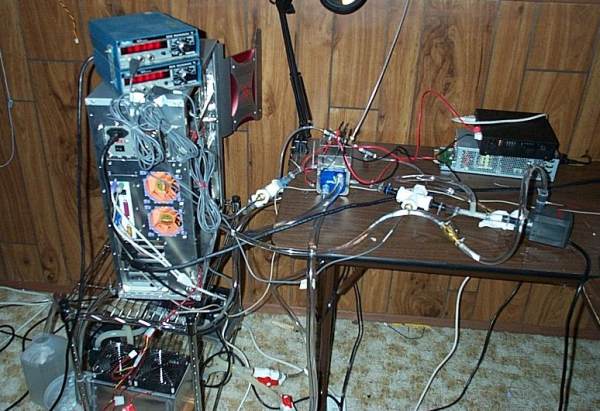 |
|
|
(note the 2 bench PSUs above right and the overall urban sprawl).
|
|
When running the MCW-Chill and associated loops noticeably heated my basement room and was very noisy. But it did get the water very cold…very rapidly.
|
|
|
|
In retrospect, one could probably get acceptable performance by using a single pump for the hot side blocks: Simply use a Y connector to split flow
from pump outlet to radiator inlets, maintain 2 loops through the hotside waterblocks, and then use a second Y to merge flow into one loop at the pump inlet (or just make a reservoir with two inlets). I had
the parts lying around though and it was probably good for at least a couple degrees C to have twice the flow rate through the heatercores. To the right you can see the hot side coolant loops.
|
|
|
|
To characterize the MCW-Chill's performance, I used the following test equipment:
|
|
- Digitec 5810 with YSI dual linear thermistors for water temperatures both in and out of the chiller and
for air temperatures on the intake and exhaust side of one of the hotside radiators.
- Maxim MAX6655 diode evaluation system with leads soldered directly to the internal diode pins of a 1700+
TBredB. Diode readings were calibrated in a water bath. MAX6655 readings were collected by a notebook computer rather than by the test system itself so that the MAX6655 software wouldn't affect CPU
load.
|
|
|
|
- Swissflow flowmeter. This sensor is rated down to -20C and has 1% error. I later compared readings from
this unit with my GPI flowmeter and there was a difference of no more than 0.01GPM over the 0.5-1.5GPM range.
- CrystalFontz 633. I used Dallas One Wire probes from this unit to measure motherboard backside and waterblock
surface temperatures, and I also used one of the 633's fan headers for the Swissflow. The 633 was controlled by a notebook computer rather than by the test system.
- Test system was a TBredB 1700+ JIUHB running on an Epox 8K3A motherboard. The 8K3A had to be modified to no
longer read from the CPU's diode so that the MAX6655 would work properly. This was done by breaking pins S7 and U7 inside the ZIF socket (An old OCWorkbench guide to modifying an K7S5A motherboard was my guide). The CPU was placed under load by using CPUBurn at high priority.
|
|
|
|
Random Forum Pic |
 |
From Thread: GPU/NB Water block (development thread) |
| ProCooling Poll: |
So why the hell not? |
I agree!
|
67%
|
What?
|
17%
|
Hell NO!
|
0%
|
Worst Poll Ever.
|
17%
|
Total Votes:18Please Login to Vote!
|
|