|
|
The Chemicals of OC'n and Super Cool'n - Insulation
|
Date Posted: Mar 24 2001
|
Author: Joe
|
|
|
Posting Type: Article
|
Category: High End Cooling
|
Page: 1 of 2
|
Article Rank:No Rank Yet
Must Log In to Rank This Article
|
|
|
Note: This is a legacy article, imported from old code. Due to this some items on the page may not function as expected. Links, Colors, and some images may not be set correctly.
|
|
The Chemicals of OC'n and Super Cool'n - Insulation By: Joe
|
The Chemicals of OC'n and Insulating your Rig
|
|
This is a topic I KNOW will help a lot of people ask on a daily basis "Where do I find This" "What's the part number for that?" "What size?" etc... Well this is going to be a multi part article. The first one is going to cover the chemicals out there to use for insulating you rig against condensation. There will be more covering water cooling components, Tools, and other aspects of the hobby. This series will all be under the name "The Chemicals of OC'n"
While I DO link to companies that sell the chemicals, or components, I in NO WAY endorse these companies. I am simply doing it to make this document as useful and complete as possible.
|
|
|
|
First lets cover the biggest group of materials - Silicone
|
|
|
|
|
In my searching for info on all the silicones out there, I found out that there are WAY too many kinds of Silicone.
The few silicones we are going to be looking at are the ones that are key to cooling and such. There are other silicones, but for the most part there is no reason to go into them.
|
|
|
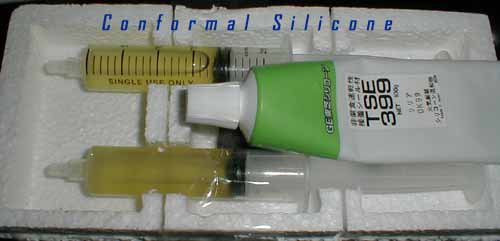 |
|
|
Conformal Silicone is pretty varied and can be very confusing due to the different terminology's used in the industry. Not many companies call it "Conformal" coatings, They use the term "Flowable" instead for the kind shown above. The other kind is commonly called "pressurized", or as it says on the blue can "Adhesive Sealant" Lets clear up another term that's thrown around a lot. RTV... What is RTV?!
|
|
|
|
RTV = Room Temperature Vulcanizing. Essentially all silicones that cure at room temp and solidify, are RTV type silicones. These are mainly 1 part silicones. There are some 2 part where you add a catalyst to solidify the silicone base, but for the majority they are all RTV types. To cure silicone compounds need Air and atmospheric moisture to work. When exposed to air the compounds in the silicone will rapidly start to solidify on the surface and slower under the surface. Its this reason that when applying RTV type silicone you should do it in thin layers, letting the first one cure fully before applying the next one. Some 2 part silicones do not need air to cure and can be put on thick and solidly like an Epoxy.
|
|
Stuff to beware of with RTV type Silicones
|
|
|
RTV silicone used improperly can actually be far worse to use in some cases then using nothing at all. Thats why this article is being wrote. The 2 issues to beware of with RTV type silicones are:
- Silicone not fully cured, or curing is Hydroscopic and will allow water to "slip through" it. It will do this until the Silicone is fully cured.
- Some RTV type sealants use Acetic Acid as part of the curing process. Acetic acid has a very vinegar like smell. ( it is the prime acid in Vinegar). This was brought to my attention after I did the RTV "Geek Gear" review and after DH2 in which I used it on the pelts and on the motherboard.
The Reason this is an issue is Acetic Acid is VERY bad for electrical components, and will destroy the inside of pelts even quicker. Not only do you have the water issue for it in a pelt, but now also the dangerous acid. This was brought to my attention by John E. Hagensieker who works as a Corrosion Control / Materials Engineering Technician on the F/A-18 Hornet program in Iwakuni Japan. He sent an email to me alerting me to this in August. It was quite a shock to me to find out how dangerous this stuff is. Here are a few quotes from the emails he sent me:
|
|
" Bottom line is that acetic acid is highly corrosive to electronics and avionics systems. The vapor produced will destroy any nearby electrical circuit where there may be dissimilar metals present. Make sure that you DO NOT use an RTV sealant that contains acetic acid or has a vinegar smell around computer interiors. Beware the blue goo until you make sure it contains no acetic acid."
|
|
"Thought it was important to pass the word on about the RTV There are many sealants from vendors that don't contain corrosives. I prefer Dow Corning myself however you have to take a look at the product Material Safety Data Sheet (MSDS) to check the ingredients."
|
|
"Here's the MSDS sheet for the 14057 Blue Goo. It doesn't flat out say it has acetic acid (this is not unusual, acetic acid isn't hazardous in the amount used and therefore doesn't have to be on the MSDS sheet by law ) in it but if you look under the firefighting section it says that the hazardous decomposition product is "acetic acid" Also if you look at the last page Under physical properties it says "Blue paste, acetic acid odor"
Don't use this stuff on motherboards, no way, no how.
I would recommend removing any from an installed motherboard and sufficiently cleaning with isopropyl alcohol and distilled water mix 50/50 any affected parts. If there is visible corrosion use a rubber eraser to remove any visible corrosion, then clean with the alcohol water mix, dry thoroughly and reassemble."
|
|
I think that pretty clearly sums all that up. SO Now lets look at what there is out there that will work good for insulating your CPU/socket/motherboard.
|
|
|
|
|
|
I do know there are more then I list below, but these seem to be the best at what they do.
|
|
|
Compressed Can Silicone RTV Sealants-
|
|
|
These are good for gap filling, and adhesive uses. These are not really flowable and are more of a toothpaste constancy or thicker. There are also some "sprays" but I have yet to find any that are Low Odor/Non Corrosive. I know there are more then below, but I am ONLY listing the ones that are specifically listed as non corrosive.
|
|
MFG
|
Desc
|
Catalog Part #
|
Company / Catalog
|
CRC Industries
|
8oz. High temperature, low odor, non corrosive gasket sealant. - Red Color
|
No. 14059
|
GrayBar
|
CRC Industrties
|
8oz. Low odor, non corrosive. Clear
|
No. 14058
|
GrayBar
|
|
|
|
|
Flowable Silicone RTV Sealants-
|
|
These are silicones that have the constancy before starting to cure of thick motor oil. This is used to coat areas of a motherboard, socket, or to let it seep into small areas to make the area air tight. I know there are more then below, but I am ONLY listing the ones that are specifically listed as non corrosive.
|
|
MFG / #
|
Desc
|
Catalog Part #
|
Company / Catalog
|
Dow Corning 784
|
10.1oz Low Odor Non Corrosive. Set time- 45min- Off White -67DegF, +300Deg F
|
74915A655
|
McMaster-Carr
|
GE 6700
|
10.1oz Low Odor Non Corrosive. Set Time 25Min- Translucent White -75DegF +400Deg F
|
7547A68
|
McMaster-Carr
|
Dow Corning 3140
|
3oz Non Corrosive, Moisture Curing. 70Min Set Time, 72 hour Cure time -49DegF +392DegF
|
7677A11
|
McMaster-Carr
|
GE TSE399-C
|
100g Tube Fast cure. Cures to a soft but strong elastomer.
|
TSE399-C
|
GE Silicones
|
Dow Corning 1-2577
|
2 syringes of 20ml of Silicone in each. Low Order, non corrosive. -67DegF +392DegF
|
1-2577
|
OCTools.com
|
|
|
|
|
Non-Flowable Silicone RTV Sealants-
|
|
These are good for gap filling, and adhesive uses. These are not flowable and are more of a Toothpaste/Gel constancy or thicker before Set. Non Flowable type silicones tend to be a stronger more resistant Sealant.
|
|
MFG / #
|
Desc
|
Catalog Part #
|
Company / Catalog
|
GE 162
|
10.1oz Non Corrosive sealant meant for Electronics work. Meant to seal IC's, an Electronics. Set time 4 hours Full Cure 48 hours. -75DegF +300DegF
|
74935A66
|
McMaster-Carr
|
Dow Corning 3145
|
10.1oz cures to a High tensile strength silicone flexible elastomer. ( Expensive - 77$) meant for electrical uses. - Clear -49DegF +392F Set 70min Full Cure 48 hours.
|
7547A68
|
McMaster-Carr
|
Loctite Ultra Series
|
10.1oz High strength Sealant meant for gasket sealing engines. -65F +400F Comes in a Aerosol can spray AND Tube
|
Aerosol- 6641A35 Tube- 75115A65
|
McMaster-Carr
|
|
|
|
|
While not nearly as complicated as picking a silicone compound, picking a neoprene to us is quite simple.
Neoprene Foam rubber come in multiple sizes, shapes, firmness ratings, and density. Tensile strength is also a variable, but not really a concern when sealing a motherboard.
There are 3 main kinds of Neoprene.
- Closed Cell Foam
- Open Cell Foam
- Neoprene Rubber
The kind we want to use in this hobby is the closed cell foam. Open Cell foam is terrible for insulation as it "breathes" and lets the moist air come in contact with the cold parts of the cooling setup, which negates even putting the foam there. Neoprene Rubber is a solid mass, not terribly flexible, or good for our uses.
My take on it is to use a thicker, and softer neoprene for under the core in the socket to allow it to form to the inside if the socket and the bottom of the core. In the picture to the right you can see how fine grain the surface is, and how small the air pockets are, this makes neoprene very soft, and very easy to form to objects.
|
|
|
|
|
|
|
|
|
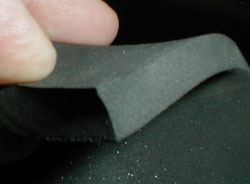 |
|
|
You can see the Closed cell foam surface
|
|
|
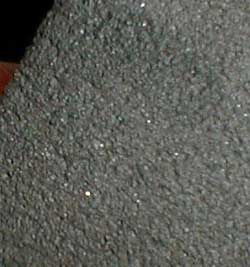 |
|
|
|
On the Pro/Mini Neoprene was used along with a flowable silicone sealant to make the cold plate and cpu socket. You can see the oversized slug inside the socket, that I compressed down to make the most air tight area under the socket.
|
|
|
|
Here is a lil firmness chart I ripped from mcmaster:
|
|
Now that we all know what it is and what its used for, now lets see where and what you should buy for this.
|
|
I am going to list 3/8" thick neoprene sheets from McMaster. They are one of the only places I know that sells such a varied selection of neoprene. Check out page 3137 if you are looking for something I don't list below.
|
|
Desc
|
Catalog Part #
|
Company / Catalog
|
Closed Cell, Firmness 3, 3/8" Thick, 42x72" sheet -70DegF +200DegF
|
8647K55
|
McMaster-Carr
|
Closed Cell, Firmness 4-5, 3/8" Thick, 42x72" sheet -70DegF +200DegF
|
8647K75
|
McMaster-Carr
|
Closed Cell, Firmness 3, 3/8" Thick, 42" x Per Lin Ft. sheets -70DegF +200DegF
|
8647K25
|
McMaster-Carr
|
Adhesive Back, Firmness 4-5, 3/8" Thick, 25'x2" strip -40DegF +160DegF
|
8694K84
|
McMaster-Carr
|
|
|
|
|
Random Forum Pic |
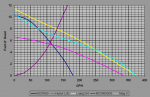 |
From Thread: What would be a step up from a MagDrive3 |
| ProCooling Poll: |
So why the hell not? |
I agree!
|
67%
|
What?
|
17%
|
Hell NO!
|
0%
|
Worst Poll Ever.
|
17%
|
Total Votes:18Please Login to Vote!
|
|