|
|
#Rotors Waterblock review
|
Date Posted: Apr 22 2004
|
Author: pHaestus
|
|
|
Posting Type: Review
|
Category: H2O and High End Cooling Reviews
|
Page: 1 of 1
|
Article Rank: from 1 Readers
Must Log In to Rank This Article
|
|
|
Note: This is a legacy article, imported from old code. Due to this some items on the page may not function as expected. Links, Colors, and some images may not be set correctly.
|
|
#Rotors Waterblock review By: pHaestus
|
|
#Rotor Waterblock Review By: pHaestus 4/22/04
|
|
|
The pin-grid blocks made by #rotor are somewhat of an anomaly in the water cooling world. Whereas many waterblock designers and end users argue
about whether new block designs are "clones" or merely "derivative", #rotor has taken a different approach. In the style of open source software, #rotor has produced a thriving community of "open source" shade
tree machinists by making his waterblock designs and machining experience freely available on his website and our forums. The internal structure of the block is
produced with a drill press and a Dremel, making it possible for those without CNC and end-mill access to still produce waterblocks on our own. If you lack those tools or simply prefer to support a small
waterblock designer, then #rotor also has a web store and is happy to custom build waterblocks to your specifications.
|
|
|
|
The block tested is an all-copper Socket-A waterblock that has a single inlet and outlet with 1/2" quick disconnect fittings on it (for 3/8" ID hose). The
block was actually in use by #rotor prior to testing, and was originally designed for TEC cooling rather than straight water cooling. Here's what #rotor had to say about the block:
"The Turbunator (A.K.A The #Rotor-Block) is the product of about 4 years worth of intensive block building, tuning, testing, overclocking and development,
all be it with a virtually non-existent R&D Budget. From there the methodology that enables practically anybody to obtain Maximum Thermal Performance for the work, Material and effort involved. The Manufacturing
process came from not having a lot of funds to acquire some expensive Milling equipment. I had to devise a way to manufacture internal geometry in a block that would lend itself to high thermal performance, but also be modular,
in that I wanted to be able to manufacture blocks of all different shapes and sizes. Obviously, the pin-grid method lends itself well to both.
This Block in particular was designed for use with a 40mmx40mm Drift0.8 TEC (172w) and from its admirable performance (in my opinion) it can be seen that
even though it's not optimized for pin-point cooling, it still has the ability to handle small core applications. In short, the aim of the design method is simple and straight forward.... Get the maximum performance and
usability for minimum effort and manufacturing costs. I am pleased to say that I've accomplished my goals and then some....."
-Michiel Mitchell (#rotor) of Superior Cooling Methodologies
|
|
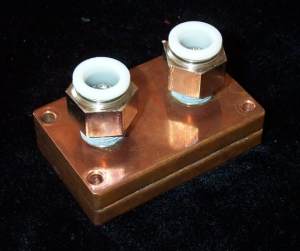 |
|
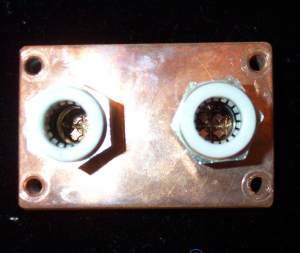 |
|
|
|
|
|
|
|
Two things stood out when I inspected this waterblock: It's a big hunk of copper (and quite heavy) and it's homemade but of obviously high quality.
Plumber's Goop was used to seal the block rather than a solder or an o-ring, groove, and bolts. This makes for a lower cost mating method for those of you without a torch or a mill, but makes cleaning the block a bit more
of a hassle (though not as much as soldering would be).
The base plate finish of the #rotor block was quite tolerable; it had been hand lapped to I'd guess 600-grit or so.
|
Test Results and Observations
|
|
Testing methods are the same as used in earlier waterblock reviews. One new development is the estimation that my
TBredB 1700+ at 13x175fsb and 1.85V (BIOS) generates approximately 73W under load. I am hesitant to convert the graphs from deltaT to C/W as of yet (still playing with this sort of W estimation), but that should give you a ballpark number for CPU power. Rather than use the included springs from #rotor, I used the same mounting hardware used in RBX,
Whitewater, Maze4, and Cascade testing.
The first test I conduct is the variation of waterblock performance over many mounting replicates at 1.50GPM flow rate.
|
|
Over ten mountings I managed a deltaT standard deviation of 0.38. I seem to be getting a bit better at block mounting and thermal paste
application. There were no surprises here or problems with mounting the #rotor block.
The next test conducted is the relationship between waterblock performance and flow rate:
|
|
The variation of performance as a function of flow is similar in shape to that of the MCW5000A: Good performance at low flow rates but little
improvement as flow rates increase above 1GPM. This makes sense when you consider that the baseplate of both blocks are fairly thick and that neither block has a central inlet to create a die area impingement effect over
the CPU core. It is useful to plot the performance of the #rotor block versus other blocks I have tested:
|
|
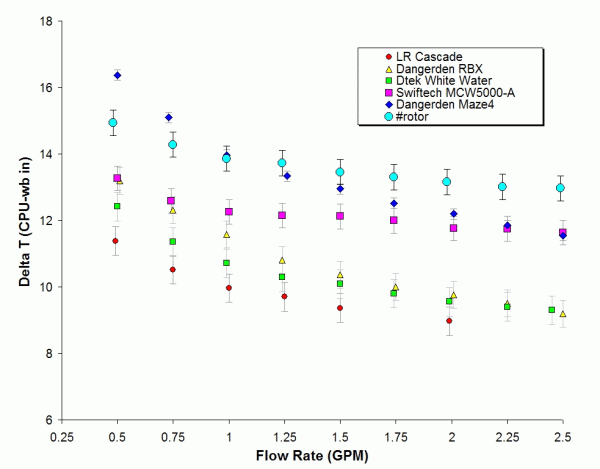 |
|
This graph is becoming less and less useful as I test waterblocks of widely differing design. I freely admit that I need to produce head loss
vs. flow rate graphs for the waterblocks I test; this information would allow us to make "apples to apples" comparisons.
Nonetheless, one can clearly see that the performance curve of #rotor's block is shaped the same as the MCW5000A, but the #rotor block as tested performs about 1.5 to 2C worse. This is in contrast to Bill Adams' testing of a similar DIY block at Overclockers.com. In Bill's testing, the DIY block performed similarly to the MCW5002 (C/W of ~0.21 in both cases). What this implies is that there is quite a bit of
design factors to consider when making a pin grid waterblock.
One of the design parameters that stood out when examining this block is the shape and spacing of the pins. The pin-fin design as implemented with drill
press and Dremel makes for a larger spacing between fins than does the diamond pin array that Swiftech uses in their MCW5000 series waterblocks. As one changes the diameter of drill then one also changes flow restriction,
surface area, and the amount of copper in the block. It is also possible to produce pins of different shape (Owen's block on Overclockers.com had octagonal pins whereas #rotor's are diamond-shaped). The other important variable to consider is base plate thickness; both parameters should all be optimized to get the most out of this waterblock style.
Perhaps someone from the forums with free time would be interested in producing a range of blocks for me to test and evaluate these variables?
Thanks again to #rotor for sending this block to review.
|
|
|
|
Random Forum Pic |
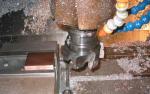 |
From Thread: waterblock design |
| ProCooling Poll: |
So why the hell not? |
I agree!
|
67%
|
What?
|
17%
|
Hell NO!
|
0%
|
Worst Poll Ever.
|
17%
|
Total Votes:18Please Login to Vote!
|
|